When DuPont needed to find innovative ways to show the unique capabilities of their advanced materials, they came to 219 Design. The partnership began in early 2018 with a concept generation session and has progressed to the development of a variety of prototypes that showcase many of DuPont’s advanced materials with novel designs.
DuPont Silicon Valley Technology Center (SVTC)
The DuPont SVTC is home to four labs to work in partnership with local customers for their prototyping, fabrication, characterization, and reliability to drive new products in relevant applications such as consumer electronics, EV/HEV/autonomous vehicles, 5G technologies, wearables, and smart materials/smart cities.
Customized AR Headset for DuPont
219 developed an open-source AR design with advanced materials and custom electronics.
Client Vision
To Invent a Better N:ow
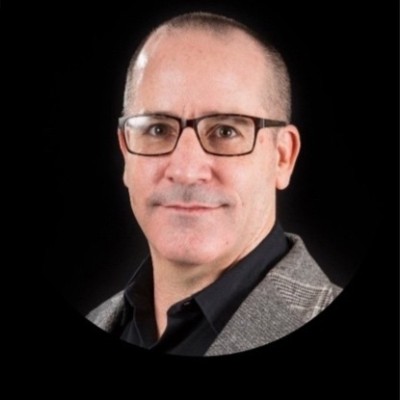
“The folks from #219Design are simply the best in the business.”Russell Arthur Rogers, Global Innovation Leader
DuPont
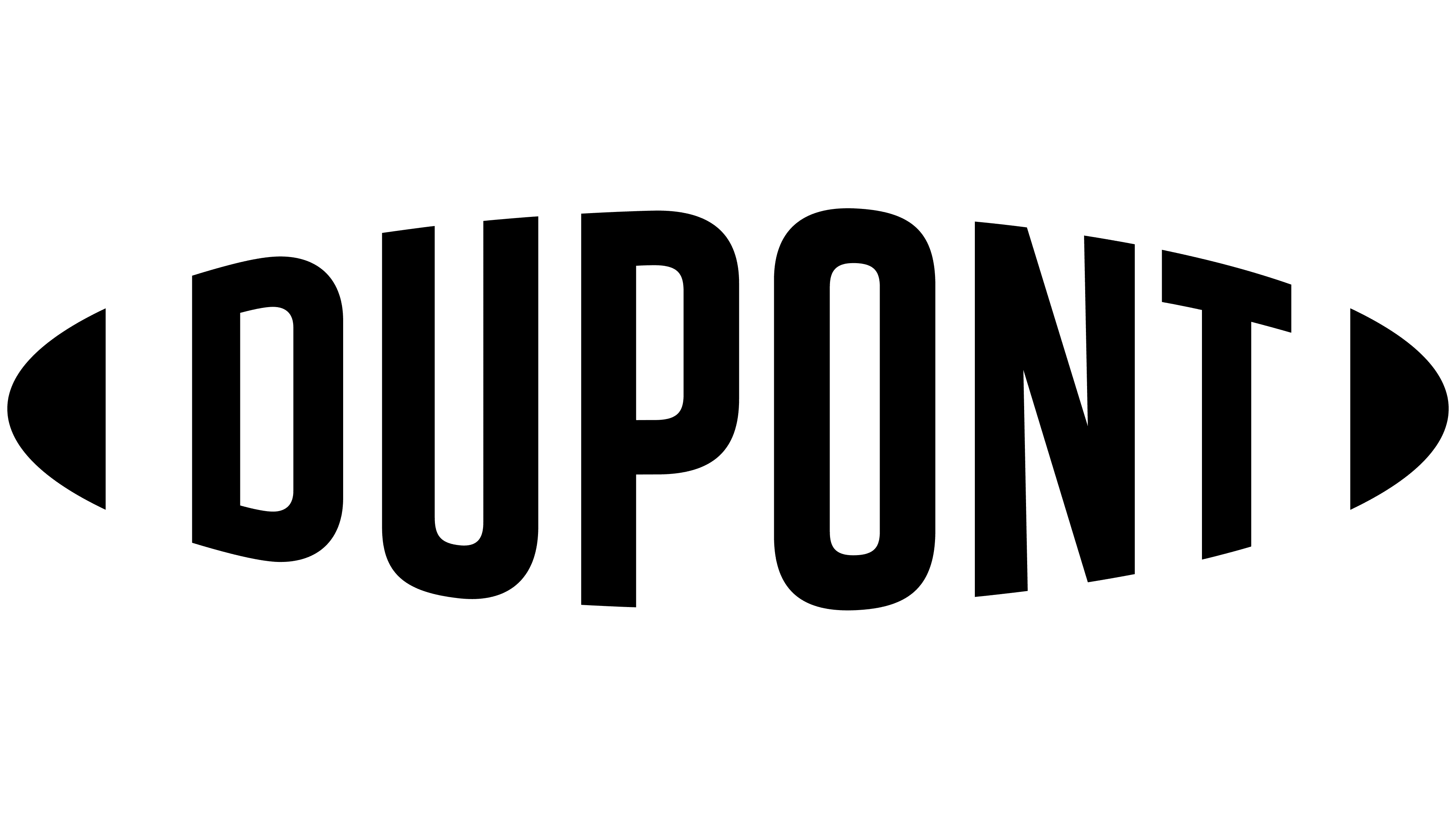
The AR Headset
219 also worked with DuPont to create an AR headset using the LeapMotion Sensor and the open source Project North Star Kit. AR and VR are some of the most exciting fields in tech at the moment and the headset showcases how DuPont materials can be used to build a bridge to the future.
The Hardware: The Project North Star open-source kit gave us a template to work from that was already compatible with standard game engines. This allowed us to prototype much more quickly than building a headset from scratch.
The Software: The LeapMotion sensors were able to recognize hands in space and display them as animations. We decided to show the user a spinning DuPont logo above their hands to display the capabilities of the headset and intuitively keep the users hands in view of the sensor, thus providing a better user experience.
Advanced Materials
- 3D printable Zytel® nylon
- 3D printable Hytrel® thermoplastic elastomer
- 3D printable carbon-reinforced-Zytel®
- Pyralux®LF flex circuit materials