2018 was the Year Of The Scooter. Funding was pouring in and competition was fierce. Skip came to us in March with the goal of winning one of the two coveted permits allowing scooters in San Francisco. Thanks to 219’s speed and agility, Skip beat out competitors (including Uber and Lyft) to win the permit in August.
About Skip
Skip Scooters was founded in late 2017 by the creators of Boosted Boards, also a client of ours. In 2018, Skip emerged from Y Combinator with a lot of potential for their last mile transportation. They enhanced the user experience by offering quality scooters, classes, and support. At the time, the other players in the scooter industry were experiencing scooter dumping, vandalism and theft were rampant, and dissenters were throwing scooters into the Bay. Skip wanted to work closely with cities to ensure a smooth rollout, and this was reflected in their project requirements.
Second Gen Scooter for Skip Scooters
Balancing the Need for Speed and Quality
Client Vision
To Become an Innovator in the Electric Scooter Space
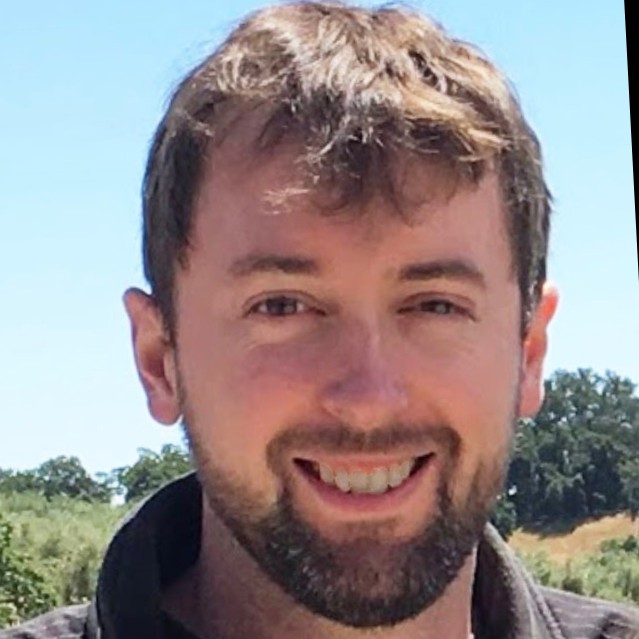
“The team at 219 was thoughtful, motivated, and committed throughout development – offering innovative ideas that showed they took my customer’s interests to heart.”Paul Nangeroni, Head of Product Engineering
Skip Scooters
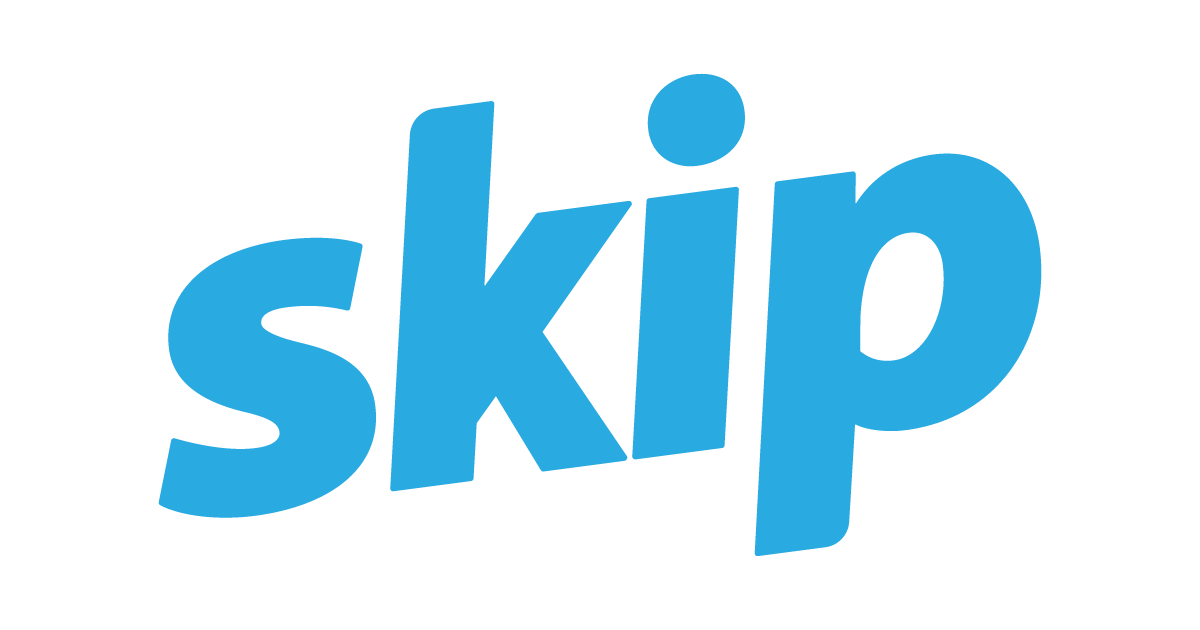
The Challenge
During the scooter-sharing expansion, speed to market was the key to success. Customers rarely sign up for a second scooter service, so the first to deploy a fleet got the business. Skip had an internal engineering team that was already working at max capacity. While they focused on the app and logistics, 219 Design played a critical role in the development of scooter hardware and software.
The scooter rental market was moving so fast that Skip didn’t have time to develop their own custom scooter. In order to quickly meet demand, all the systems had to be retrofitted into an off-the-shelf consumer scooter and still be reliable in outdoor, public streets throughout the United States. Our electronics would have to communicate with and control the existing throttle, lights, and peripheral hardware. Our mechanical system would have to bracket into the constraints of the existing scooter. But the real challenge was moving fast and quickly iterating on a design that could be scaled up and deployed at an extremely aggressive rate. As Skip gained experience with their deployed fleet, they added additional requirements – some examples included anti-theft features, water tightness, and over the air updates.
While the retrofit effort was critical to quickly scaling the Skip fleet, the need for an integrated lock became the key to winning permits in key locations such as San Francisco.
Integrated Lock Challenge
In order to win one of the two coveted San Francisco scooter permits, the San Francisco lock requirements stated that “all powered scooters shall have an integrated locking mechanism which cannot be removed using simple tools and which securely holds the scooter upright when parked at a bike rack or other fixed object.” Skip and 219 developed a strategy to ensure scooters would be properly parked and not block the right of way. Applying for the permit put a five month deadline on the lock development. In addition, Skip wanted their scooter to be unlockable via the cloud, sense if it was locked or unlocked, and be rapidly scalable.
Smart Lock Design Phase
219 Design developed and prototyped a smart lock to integrate with the scooter design. All disciplines were on deck for this project. Despite the rush, 219 Design was able to quickly build in quite a few awesome features. In addition to meeting all the San Francisco permitting requirements, the lock was retrofittable, scalable, and reliable. The lock was centered in the scooter allowing use from either side, and lock tip sensing technology would enable feedback to Skip and users about whether the lock was securely engaged. This design would allow Skip to further nudge users to properly stow their scooters, even beyond the San Francisco requirements.
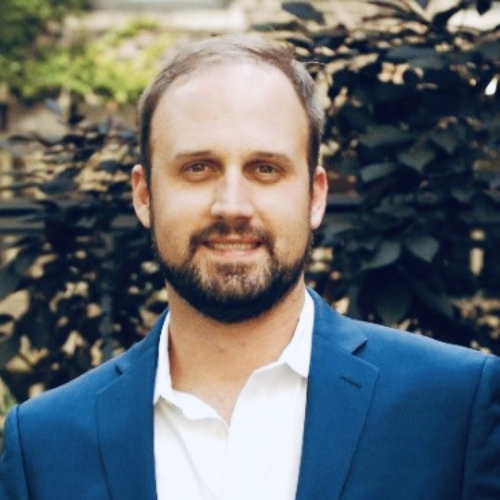
“We were excited to step up to the challenge and meet the aggressive timelines needed to make this project a success and thrilled to see Skip achieve their goal of winning the San Francisco permit.”Trevor Wesolowski, Senior Mechanical Engineer
219