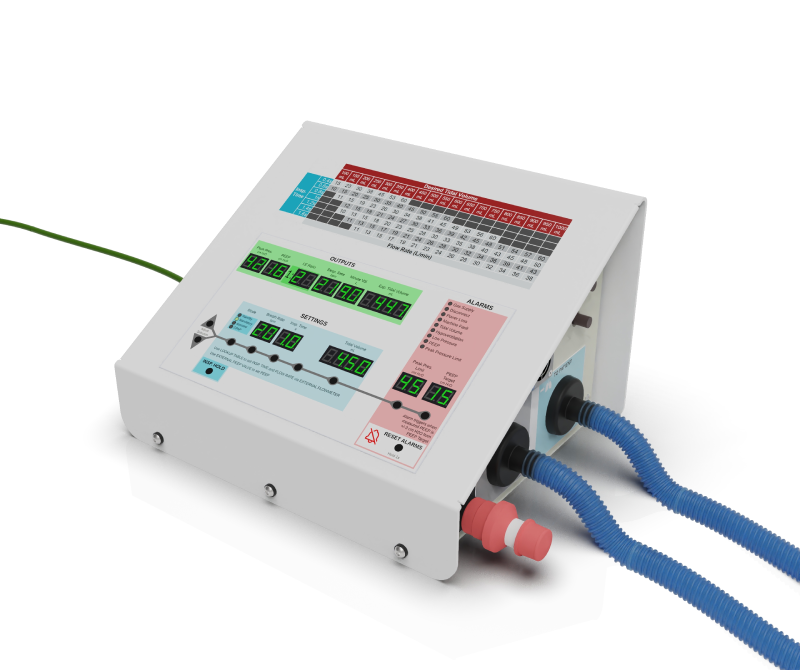
Just days before the U.S. Food & Drug Administration (FDA) issued an umbrella Emergency Use Authorization (EUA) in response to concerns about the insufficient supply and availability of FDA-cleared ventilators to treat patients during the COVID-19 pandemic, we got a call from friends at Stanford University’s CamLab. They wanted to increase the supply of ventilators by designing a simplified, streamlined version that required fewer parts and less time to make – with the goal of getting ventilators into hospitals where there wouldn’t otherwise be any. Fortunately, 219 Design already had experience developing the OneBreath ventilator and other high stakes medical systems. Six months later, O2U Inc., the company established to develop and distribute this new ventilator, submitted the design to the FDA for emergency use authorization.
UPDATE: On March 22, 2021, the O2U ventilator received FDA Emergency Use Approval!
“During public health emergencies, FDA can use emergency authorities, including Emergency Use Authorizations (EUAs), to help make medical products available as quickly as possible by allowing unapproved medical products to reach patients in need when there are no adequate, FDA-approved and available alternatives. These products may include tests to help diagnose diseases, critical medical devices needed by patients or healthcare personnel in the context of a public health crisis, and drugs to be used in an emergency to diagnose, treat, or prevent serious or life-threatening diseases or conditions.”
Understanding the Emergency Use Authorization
Within a week of receiving that call, engineers from 219 Design began working in close virtual collaboration with physicians, respiratory therapists, academics, and industry professionals who also wanted to help. Developing a medical device specifically for emergency use authorization was a first for us and a learning experience.
We started with the Criteria for Safety, Performance, and Labeling. At that point, the group had to make a decision about the future of our ventilator. We determined that our design was intended to exist after the EUA phase had passed. As a result, it required some extra thought to its usefulness in the long term. The effort also required funding. Chan Zuckerberg Biohub and Eleftheria Foundation stepped in to finance a significant portion of the development.
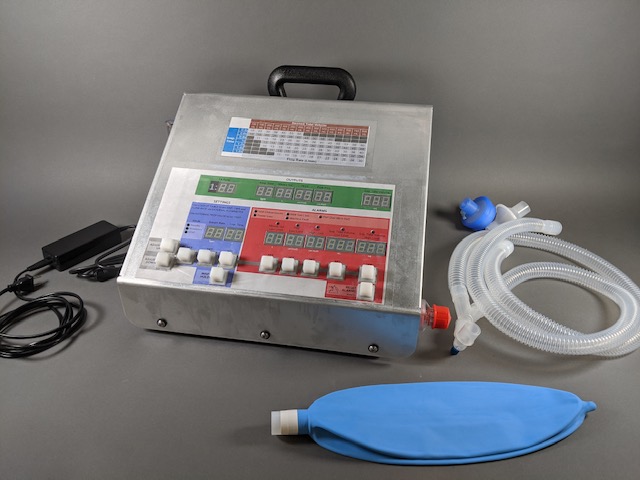
The Biggest Challenges
The most significant design challenges were around supply chain and time limitations as well as COVID itself. We wanted a simple design that would be easy to source and build. We also wanted the ventilator to be affordable and reliable.
“…the current emergency climate has catalyzed alternative designs that might enable greater flexibility in terms of supply chain, manufacturing, storage and maintenance.”
A low-cost, rapidly scalable, emergency use ventilator for the COVID-19 crisis
Designing a Solution
The best products are designed to solve problems and the O2U ventilator is no exception. This solution is affordable, reliable, and easy to build. In addition, the functionality is able to carry a patient from hospital admission to discharge with one breathing device.
There were two design choices that led to the most impactful differences between this design and other ventilators – the reliance on externally pressurized and mixed gas and the pressure-limited-time-cycled mode of ventilation. The resulting design requires far fewer parts and allows for use in both non-invasive and invasive modes. In the non-invasive mode, the ventilator works much like a CPAP system. The invasive ventilation modes are for intubated ventilation. The benefits of this design as a single ventilation platform include reducing the number of devices medical professionals need to work with and maximizing the familiarity they have with the device.
“The goal of this device is to allow a patient to be treated by a single ventilator platform, capable of supporting the various treatment paradigms during a potential COVID-19 related hospitalization.”
A low-cost, rapidly scalable, emergency use ventilator for the COVID-19 crisis
Dramatically Accelerated Timelines
In a typical scenario, there are clear project, regulatory, and compliance requirements. However, when it comes to designing a device for emergency use, a careful risk/benefit analysis must be done to determine where it will be compliant and where it won’t. It was also important for us to understand how the design decisions we made during this process would impact our ability to satisfy the requirements before we started working on the design. Since our ventilator was designed from scratch and we wanted to get it into hospitals as quickly as possible, our focus was on meeting the requirements that provided the most benefit to patients. This approach allowed us to reduce the development time significantly.
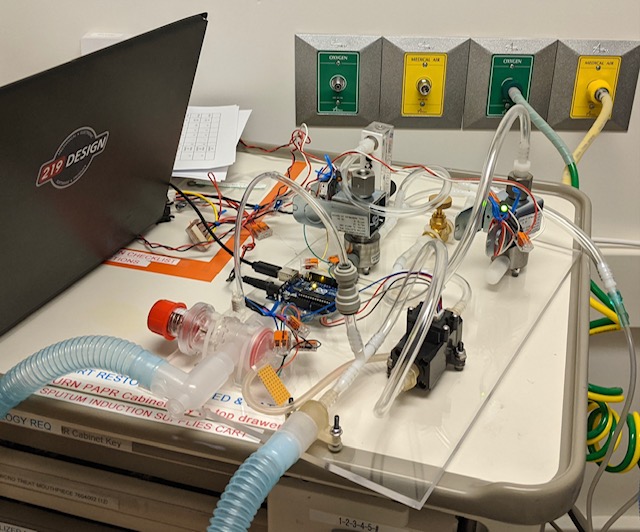
Supply Chain Limitations
Soon after we started this project, the demand for ventilators went through the roof and components commonly used in ventilators became very hard to find. With this in mind, a working model was formed using readily available parts that we hoped would be immune to the supply chain issues plaguing many other ventilation products. From there, we began to rapidly iterate to improve to the design.
COVID Challenges
In 2013, we began working with OneBreath on a reliable and low cost ventilator. This ventilator was designed to be globally accessible. As a result, it is optimized for low resource environments and designed for novice through advanced users.
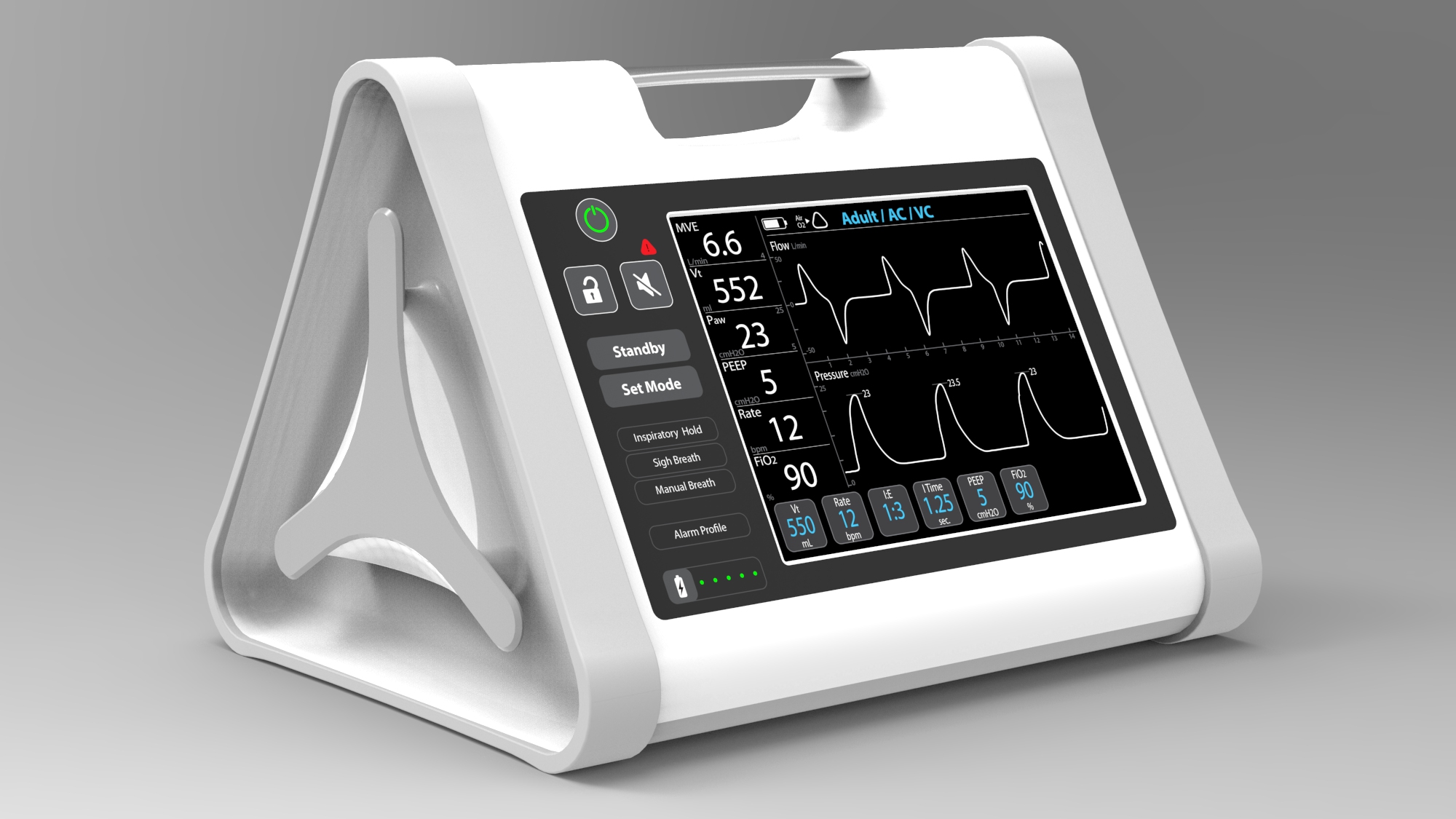
The biggest difference between the two development scenarios was having the time to interact with users. For OneBreath, a 219 team member flew to India (the first target market for the device), visited hospitals, and interacted with users. There were many renderings, foam mockups, and functional prototypes that were evaluated before the design was finalized. While designing the O2U ventilator, we had access to many respiratory therapists and pulmonologists to inform our design. However, due to the compressed timeline and COVID safety measures, our opportunities to sit down with them in person to interact with prototypes were limited. Video calls, recorded videos, and collaborative online documentation tools enabled us to gather additional user input.
“While there are a lot of similarities between our design process for the ventilators, the circumstances under which they were designed were very different. The O2U ventilator was designed in a matter of months whereas the OneBreath ventilator was designed over the course of many years.”
Larry Miller, Co-founder, 219 Design
While our interdisciplinary team typically works together in the same physical space, COVID safety measures made it necessary for our software, mechanical, and electrical engineers to take turns in the office. Pictured below is a rare instance where two 219 Design partners came together to tackle a design challenge.
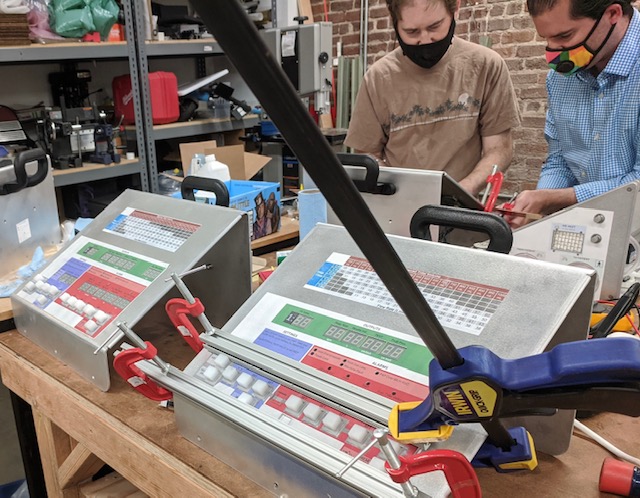
Next Steps
O2U Inc. plans to engage a contract manufacturer that is certified to produce medical devices and will implement GMPs (Good Manufacturing Processes) as outlined by the FDA. Under these strict guidelines, the devices will be manufactured reliably.