This collaborative effort between 219 Design, Stanford, CZBioHub and others is a success story about overcoming challenges encountered in new product development. COVID created a host of significant and varied challenges around designing for EUA approval, supply limitations, a distributed and virtual team, and an accelerated timeline. This team successfully tackled them all, resulting in an FDA Emergency Use Authorized ventilator.
About O2U
O2U, Inc. originally got its start at Stanford University. The Stanford Bioengineering department is an interdisciplinary division of the engineering school, making it the perfect place for a talented team to come together in a time of great need to develop this low cost, single use ventilator.
That’s exactly what happened at the start of the COVID pandemic. Just days before the U.S. Food & Drug Administration (FDA) issued an umbrella Emergency Use Authorization (EUA) in response to concerns about the insufficient supply and availability of FDA-cleared ventilators to treat patients during the COVID-19 pandemic, we got a call from friends at Stanford University’s CamLab. They wanted to increase the supply of ventilators by designing a simplified, streamlined version that required fewer parts and less time to make – with the goal of getting ventilators into hospitals where there wouldn’t otherwise be any.
Fortunately, 219 Design already had experience developing the OneBreath ventilator and other high stakes medical systems. Six months later, O2U, Inc., the company established to develop and distribute this new ventilator, submitted the design to the FDA for emergency use authorization. About six months after that, on March 22, 2021, the ventilator received Emergency Use Approval from the FDA.
Rapid Response Ventilator for O2U
Developing for Emergency Use
Client Vision
To Save Lives by Addressing a Critical Need in our Healthcare System
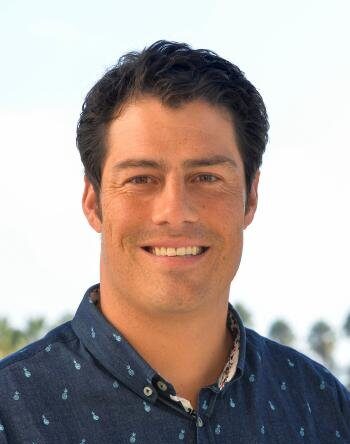
“I have the utmost respect for the 219 Design team who are incredibly dedicated, creative, and hard working. They are not typical consultants who are just doing work for hire, they joined us in our mission and worked tirelessly to help our end customer, patients sick from COVID-19. There is no way we could have taken O2U ventilator from concept to FDA approval in less than 1 year without them.”David Camarillo, Co-Founder
O2U
Overcoming COVID Specific Challenges
Today, thankfully, the need for ventilators has decreased in much of the world relative to the early days of the pandemic. However, the learning from this process will live on in future projects. There are always challenges when developing a brand new product. For this project however, our biggest challenges weren’t technical. Designing for EUA was a first for most, if not all of us on the team. Designing around supply chain limitations required creativity. We were lucky to have a diverse team of experts but it was highly distributed and had to be exclusively virtual. Luckily, ambiguous environments are our speciality so we anticipate change and roll with the punches.
Emergency Use Authorization
The first decision we had to make was whether or not our device was intended to live beyond emergency use. Deciding that it was set us on a very different path than the alternative.
There were two additional design choices that led to the most impactful design differences between this and other ventilators – the reliance on externally pressurized and mixed gas and the simplified time-cycled mode of ventilation. The resulting design requires far fewer parts and allows for use in both non-invasive and invasive modes. In the non-invasive mode, the ventilator works much like a CPAP system. The invasive ventilation modes are for intubated ventilation. The benefits of this design as a single ventilation platform include both reducing the number of devices medical professionals need to work with and maximizing the familiarity they have with the device.
Supply Limitations
The O2U ventilator was designed specifically to solve current problems around the supply chain shortages and time to build. As we were designing the ventilator, we were seeing the components commonly used in ventilators become harder and harder to find. With this in mind, we developed a functional prototype using readily available parts we hope will be immune to supply chain issues now and in the future.
Distributed Team
219 Design began working in close virtual collaboration with physicians, respiratory therapists, academics, and industry professionals within days of that first call. Luckily, we already had the tools in place for a distributed team to communicate, document, and share. We use a communication tool, developed internally at 219 Design, that allows us to see where people are in a virtual office environment, instant message via Slack, and set up instant video calls via Google Hangouts.
Accelerating Product Development
In a typical scenario, there are clear project, regulatory, and compliance requirements. However, when it comes to designing a device for emergency use, there is some tolerance for devices that don’t satisfy every requirement as long as justification for the deviation and it is proven that the patient’s safety is not compromised. Therefore, a careful risk/benefit analysis must be done to determine which requirements can be safely worked around for the sake of bringing the device to production in a shorter time. It was also important for us to understand how the design decisions we made during this process would impact our ability to satisfy the requirements before we started working on the design. Since our ventilator was designed from scratch and we wanted to get it into hospitals as quickly as possible, our focus was on meeting the requirements that provided the most benefit to patients. This approach allowed us to reduce the development time significantly.
Mission Accomplished
The solution is a low cost, rapidly scalable, versatile, emergency-use-authorized ventilator that supports various treatment paradigms, enabling many patients to be treated by a single platform. This one-device-one-visit solution supports a patient throughout their treatment. This ventilator is also immune to current part shortages and can be assembled quickly.
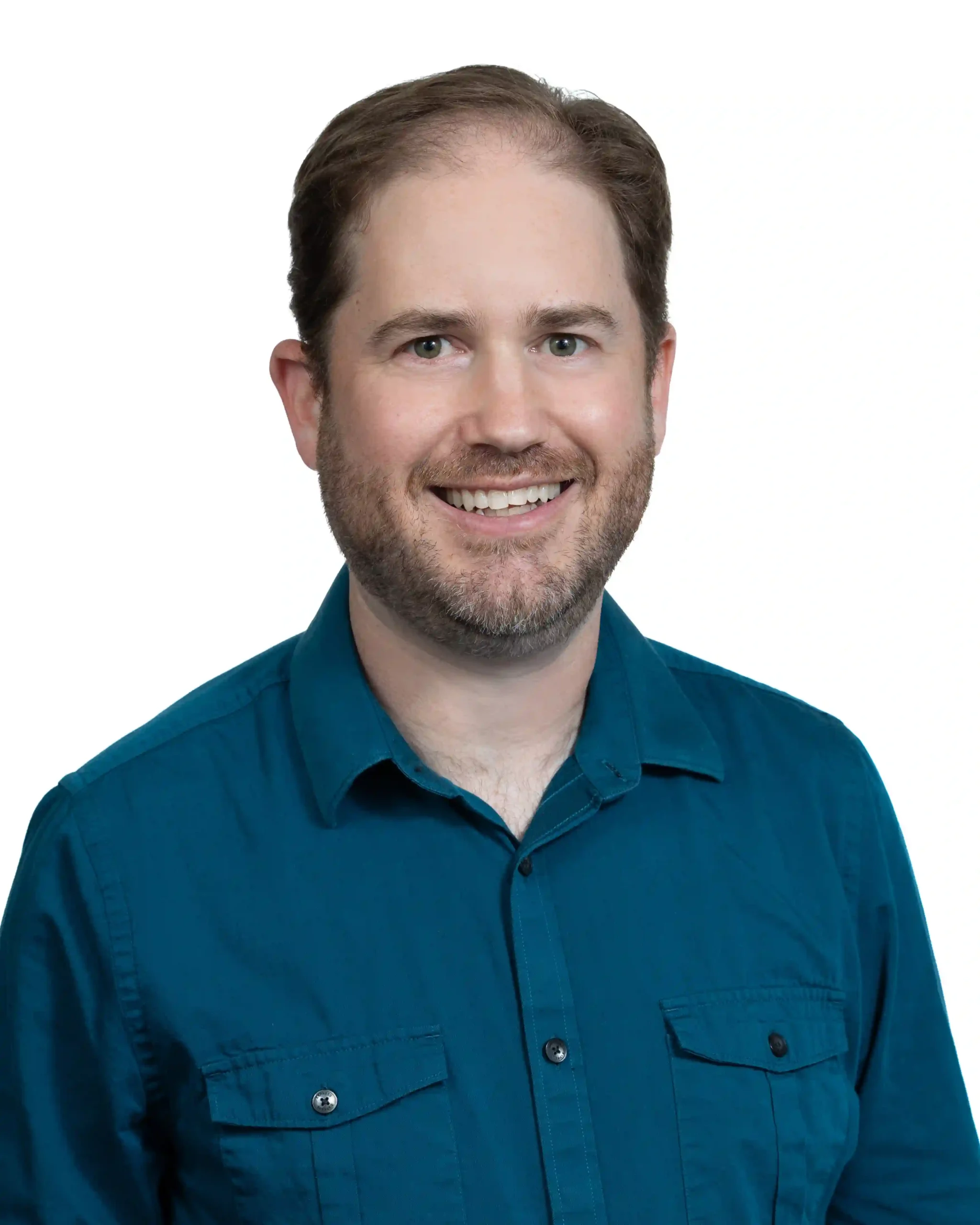
“It was wonderful to be able to do something as important as developing the O2U ventilator at a time when we all felt very helpless at the start of the pandemic. Working on this project was an honor.”Larry Miller, Founding Partner
219